Ventilators are crucial for keeping severe COVID-19 patients alive. Manufacturers won't let hospitals fix them without paying hefty fees.

- Facing a ventilator shortage at the peak of the first pandemic wave, hospitals needed to keep their devices running.
- Ventilators are crucial for helping patients with severe COVID-19 cases, helping their lungs work as the virus attacks their bodies.
- But like all medical devices, ventilators require regular maintenance and fixes.
- Manufacturers place restrictions on the devices, requiring technicians to undergo expensive training and pay for access to manuals in order to repair them.
- Biomedical technicians say the repair process should be in the hands of hospitals, not device manufacturers.
- "Let the organizations decide what the best avenue is for maintenance on the equipment that they own," Leticia Reynolds, a biomedical technician, told Business Insider.
- Visit Business Insider's homepage for more stories.
As cases surged in March, the country had just 160,000 of the life-saving devices, prompting concerns that they wouldn't reach every patient who needed one.
In those early weeks, hospitals had to beat back the coronavirus pandemic with the ventilators they already had. The coronavirus is spread through the respiratory system, and COVID-19 attacks the lungs. In severe cases, the machines are crucial for pumping air in and out of the lungs, doing the breathing for them. Hospitals, stretched to their limit, faced a problem: How to keep their limited ventilator stock running.
Like other medical devices, ventilators require regular upkeep and repairs, which render them temporarily unusable. More maintenance time means less time keeping coronavirus patients breathing.
But technicians like Leticia Reynolds, president of the Colorado Association of Biomedical Technicians, must wade through a labyrinthine system of fees, requests, certifications, and training programs before servicing the devices.
"You can't get [ventilator] parts unless you've been to school," Reynolds, a biomedical technician who's been in the profession for two decades, told Business Insider. "You can't buy manuals unless you've been to school."
Reynolds wasn't referring to technical school. Companies host their own expensive training programs that take up time and money, frustrating technicians who needed to fix ventilators in the crisis.
"This is an issue that we face each day, whether or not there is a crisis at the time, on a variety of different types of equipment," she said.
Hospitals spend thousands of dollars to get manufacturers to approve biomedical technicians
Reynolds' hospital, the Memorial Hospital at the University of Colorado Health, owns about 50 ventilators from six different manufacturers. In preparation for COVID-19 patients, it borrowed another 30 in mid-March. The hospital has 11 different ventilator models in its stock.If an in-house technician needs to repair a ventilator, they can't just go ahead and grab their toolkit. They need the manufacturer's stamp of approval first. At Reynolds' hospital, that means 11 different certifications — one for each model.

A single certification program for one technician could cost up to $7,000, Reynolds said. That's before lost labor time and travel costs like flights and hotels.
The problem that Reynolds and others face has been taken up by the "right-to-repair" movement, which advocates the right for product owners to fix their own devices free of charge. The issue is a sprawling one: From medical devices to cell phones and tractors, companies impose software locks to prevent independent mechanics from fixing their products.
"It just isn't feasible to send a technician to a technical training on each and every device," Reynolds said. "Not only does it get costly, but it can be hard sometimes to even get into the trainings, depending on how often they are provided."

But manufacturers give the technicians and hospitals no choice. Dräger, who has sold ventilators to Reynolds' hospital, "will not give you manuals unless you've been to school," she said. After getting the certification, she said, hospitals still need to pay an annual subscription fee to maintain access to repair manuals.
Dräger did not answer questions about the fees it charges for certification and other services. "We provide 24/7 technical support to the hospitals we supply as well as rapid on-site service," a spokesperson told Business Insider.
Technicians have crowdsourced their own repair manuals
During the pandemic, some manufacturers have given their repair manuals to technicians for free on request, said Nathan Proctor, a director at the US Public Interest Research Group (PIRG).It's a welcome development, but Proctor says it doesn't go far enough. It might take weeks for manufacturers to respond to such requests, he said.
"There's a huge backlog on that side," Proctor, head of US PIRG's right-to-repair campaign, told Business Insider.
Gaining quick, easy access to repair information has been crucial for technicians during the pandemic. With help from right-to-repair advocates, technicians have compiled crowd-sourced databases, replete with repair manuals.

But the manuals that do exist are spread across the internet, Proctor said, and the hunt for a given manual could extend repair times as a coronavirus patient waits for a device that might save their life.
A technician "would be basically poking around on online forums trying to get access information without a central resource," Proctor said. Other times, the manuals cannot be downloaded at all.
Dräger's manuals can be found on one prominent crowd-sourcing website, Frank's Hospital Workshop, a resource that was established, in part, because of a lack of "technical support from the manufacturers," the founder wrote. But Dräger locked the manuals away. "Download prohibited by Dräger," the website says. "Support is not desired."

A Dräger spokesperson told Business Insider: "We provide manuals, to the extent consistent with FDA quality standards."
According to Olivia Webb, a spokesperson for IFixIt, making the manuals inaccessible is a typical "tactic" used by manufacturers. Manufacturers will often require service passwords just to reach the diagnostic readout of a particular ventilator model.
"[Manufacturers] require individual biomedical technicians to have a login key or a password to the repair manuals or the repair information or just a user manual," Webb told Business Insider. "And those are not easily shareable between other biomedical technicians."

Sometimes manufacturers share the passwords with hospitals, Proctor said. Even then, "those ventilators might be moving around the country," especially during the pandemic, he said. The login information might not get passed along with the devices — an additional hurdle if a ventilator ends up at another hospital and later needs repairs.
Some ventilator manufacturers have eased up on the requirements. A spokesperson for General Electric, another one of the world's largest ventilator manufacturers, directed Business Insider to a company webpage, which announces that GE has temporarily waived "the 4-day in-person training that GE Healthcare usually requires before providing such material."
'A biomedical technician is not just somebody walking in off the street'
The US PIRG praised GE for suspending the training programs and attendant costs. Even so, GE still insists that repairs should only be undertaken by people who have "qualifications" with servicing its devices.It's an allusion to manufacturers' core argument against the right to repair. Expert technicians, they say, need brand-specific training to do their jobs competently.
In lieu of answering Business Insider's questions, representatives for GE and Dräger told Business Insider to contact AdvaMed. AdvaMed is a lobbying firm that represents more than 400 clients, among them the world's major medical device manufacturers — like GE and Dräger, as well as Siemens and Philips. It didn't respond to Business Insider's request for comment.

AdvaMed spends a lot of its time fighting against right-to-repair legislation. It spent more than $3.8 million in lobbying efforts, according to the Center for Responsive Politics, fighting right-to-repair bills up for consideration in 20 states last year.
Each bill failed.
"The medical device industry's primary concerns with state Right to Repair legislation is that they could result in maintenance and repairs of medical devices being performed by untrained personnel, and that inappropriate replacement parts may be used," AdvaMed said in a letter to Massachusetts lawmakers considering one such bill, obtained by Vice.

Webb said the industry's argument about expertise is disingenuous.
"A biomedical technician is not just somebody walking in off the street. A biomedical technician is also trained and goes to school to repair these machines," Webb said. "So it's not like you're just giving information to anybody."
Generally, a practicing technician has an associate's degree in biomedical technology. Entry-level positions may not require such a degree, said Reynolds, "but they don't work on vents or other higher level of equipment without the hands-on training provided from senior-level technicians or manufacturer equipment schools."
Reynolds said that she — or any other trained technician — could repair equipment on her own if they had the manual, and any specialized test equipment and software to do it.
"Let the organizations decide what the best avenue is for maintenance on the equipment that they own," she said.

In March, President Donald Trump's administration promised an additional 100,000 ventilators to be delivered to US hospitals, though many have arrived only after the country's death toll surged into the tens of thousands. According to the Associated Press, many of them arrived too late, leading to a glut of unused ventilators that will now be sent overseas.
That doesn't mean that technicians' jobs have gotten easier. They must still play by the manufacturers' rules. If Reynolds can't get certified, locate the manuals, or access them, there is one final option: Send the ventilators out for maintenance.
For sick patients, that isn't a helpful solution.
"It could be up to a month before those devices come back," Reynolds said.
Join the conversation about this story »
NOW WATCH: Inside London during COVID-19 lockdown
* This article was originally published here
http://feedproxy.google.com/~r/typepad/alleyinsider/silicon_alley_insider/~3/F-0PRfb6VO0/ventilator-manufacturers-dont-let-hospitals-fix-coronavirus-right-to-repair-2020-5
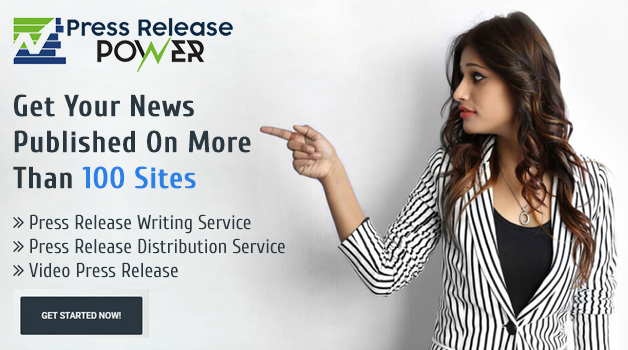
No comments